Understanding Element Flatbars: Key Insights and Applications
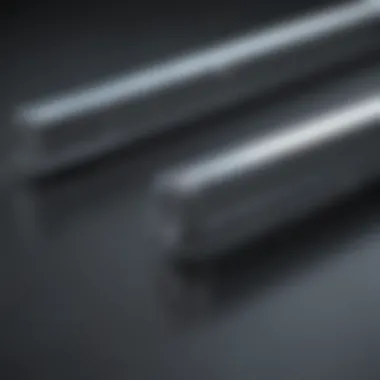
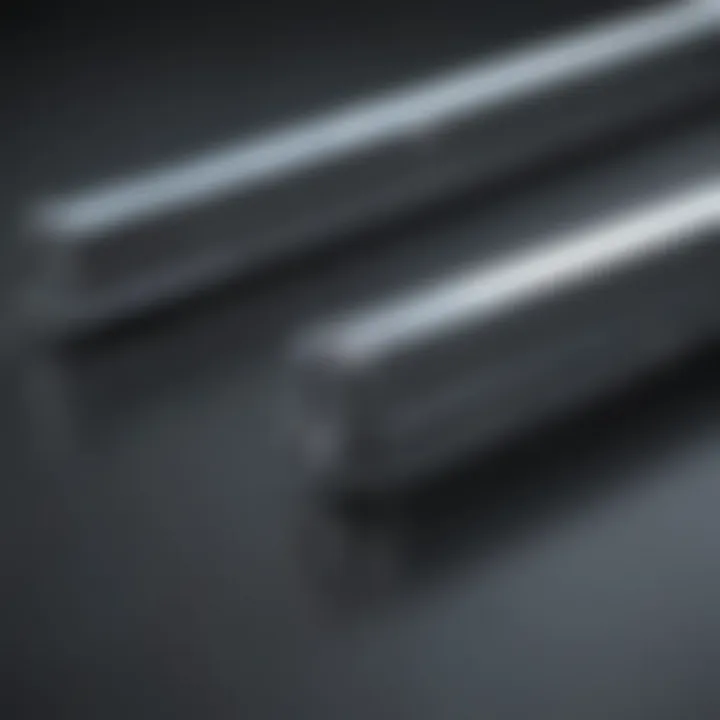
Intro
Element flatbars are essential constructs in numerous industrial settings. Their unique properties and extensive applications reveal their significance in modern manufacturing and construction. This exploration will dissect their design, functionality, and industry relevance. By understanding element flatbars, professionals can appreciate their contributions to innovation and field standards.
Fundamental Characteristics of Element Flatbars
Element flatbars are often manufactured from steel or aluminum, providing durability and strength. They typically feature a rectangular cross-section and are available in various sizes and thicknesses. The combination of flat and rectangular geometry allows for straightforward integration into diverse constructions, from structural frameworks to machinery components.
The adaptability of element flatbars enhances their usability. Whether for creating support beams, frames, or other structural units, these components are instrumental across multiple sectors, including construction, automotive, and aerospace. A deeper understanding of their material properties and usage contexts will pave the way for innovative applications, optimizing performance in various projects.
Applications in Various Industries
Element flatbars find extensive application in different domains. In construction, they provide vital support for buildings and structures. Their rigidity and reliability stand the test of time against various environmental forces. Additionally, in manufacturing processes, element flatbars are integral as components for machinery, ensuring consistent and efficient operations.
Overall, their widespread utilization speaks to their capacity to meet varied specifications and operational demands.
"Element flatbars offer a remarkable balance of efficiency and versatility, crucial for modern engineering solutions."
Technical Specifications
Understanding the technical specifications of element flatbars can significantly improve their application. Key specifications include:
- Material Composition: Most frequently utilized materials include carbon steel, stainless steel, and aluminum. Each material presents distinct advantages depending on the intended application.
- Dimensions: Variations in width, thickness, and length are essential, as they determine the load-bearing capacity and the overall strength of the flatbars.
- Surface Treatment: Coatings or treatments can enhance corrosion resistance or alter surface finishes for aesthetic purposes.
These specifications help engineers select the right type of flatbar for specific projects, thus maximizing performance and longevity.
The End
In summary, element flatbars are more than mere components. They are fundamental in numerous industrial applications and speak to the trends in engineering practices today. The intricate understanding of their characteristics, applications, and specifications can lead to better design and implementation in various industries.
Foreword to Element Flatbars
Element flatbars are fundamental components in various industries, and their significance cannot be understated. These flat pieces of metal serve a variety of purposes and are integral to construction, manufacturing, and many other applications. Understanding element flatbars provides insight into their unique characteristics and broad utility. This section introduces the essential elements and benefits of element flatbars, offering a solid foundation for deeper exploration throughout the article.
Definition and Characteristics
Element flatbars are typically defined as long, flat pieces of metal that possess uniform thickness and width. They can vary in length and dimensions depending on their intended use. Common metals used for production include steel, aluminum, and stainless steel. Each material offers distinct properties, impacting their strength, weight, and corrosion resistance.
Key Characteristics:
- Thickness: The thickness of flatbars can range to meet specific project requirements. Thicker bars provide more strength but may increase weight.
- Width: The width also varies, allowing customization for the intended application.
- Surface Finish: A smooth or textured finish can affect both aesthetics and functionality.
- Strength-to-Weight Ratio: Depending on the material, flatbars can offer impressive strength without excessive weight, making them highly desirable.
These characteristics enable element flatbars to be versatile tools in construction and manufacturing.
Historical Context and Evolution
The evolution of element flatbars is intertwined with advancements in metallurgy and engineering. Initially, flatbars were produced by blacksmiths using rudimentary tools and techniques. As industry progressed, the introduction of powered machinery enabled larger-scale production, improving precision and performance.
Historically, these elements were crucial in the development of early infrastructure. The expansion of railways and buildings in the 19th century saw a surge in demand for strong, reliable materials like flatbars. This trend continued through the 20th century with new alloys and manufacturing techniques enhancing their properties.
In recent years, the growing focus on sustainability has spurred innovations in material recycling and eco-efficient production processes. Today's element flatbars reflect a culmination of tradition and modernity, embodying both resilience and adaptability.
Materials and Manufacturing Processes
Understanding the materials and manufacturing processes behind element flatbars is crucial. This section examines the specific elements that shape the quality and functionality of flatbars. Each choice made during production adds layers of benefits but also brings considerations that need attention.
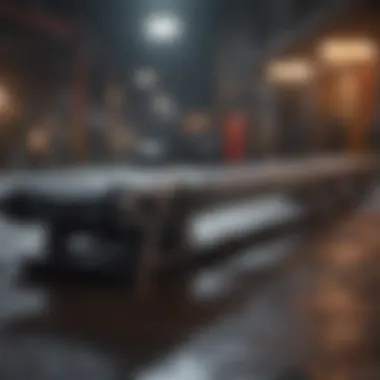
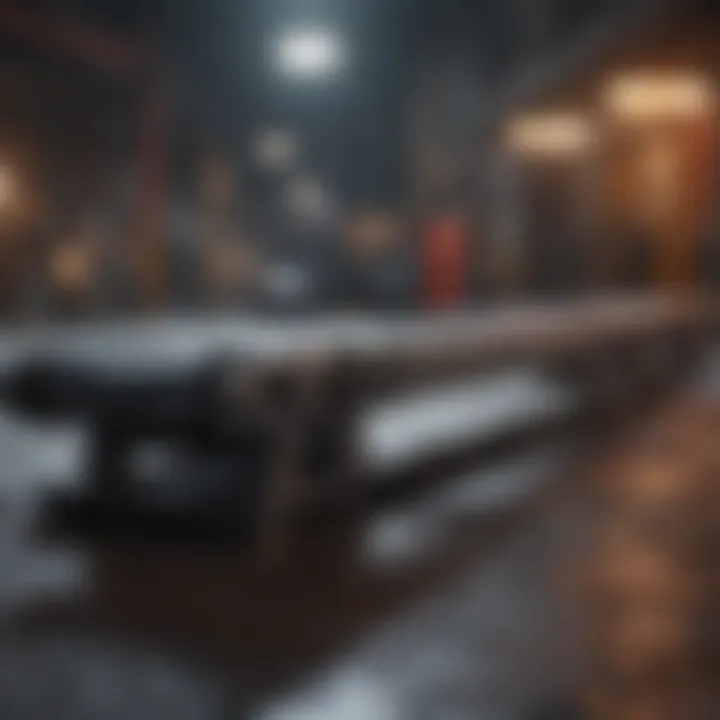
Common Materials Used
Element flatbars are primarily made from several key materials. Steel, often used for its strength and durability, is a popular option. Stainless steel, on the other hand, offers resistance to corrosion, making it suitable for harsh environments. Aluminum is chosen for its lightweight properties, providing versatility in applications where reducing weight is essential. Copper flatbars, though less common, provide excellent electrical conductivity.
- Steel: Strong and widely used. Offers great structural integrity.
- Stainless Steel: Best for resistance to rust. Ideal for outdoor or wet conditions.
- Aluminum: Lightweight and adaptable. Perfect for many applications.
- Copper: Great for electrical uses. Less common in structural applications.
Each material has its unique attributes, making it suitable for specific needs. Understanding the properties is key to choosing the right flatbar.
Production Techniques
The methods employed to produce element flatbars play a vital role in ensuring their functionality and performance. Hot rolling and cold rolling are two common techniques. Hot rolling involves heating the metal above its recrystallization temperature, resulting in a final product that can be further shaped as needed. Cold rolling, on the other hand, takes place at room temperature and provides a higher degree of dimensional accuracy and surface finish.
- Hot Rolling: Good for shaping large amounts of metal. Less precise but cost-effective.
- Cold Rolling: Higher accuracy. Best for tight tolerances and surface quality.
Understanding these techniques informs the selection process for manufacturers depending on the application demands.
Quality Control Standards
Quality control is not just a regulatory formality in manufacturing; it is a fundamental process that guarantees the integrity of element flatbars. Standards such as ISO 9001 ensure that products meet customer and regulatory requirements. Testing procedures like tensile testing and impact testing are common. They ensure that flatbars can withstand the forces they will encounter in actual usage.
Quality must be maintained throughout the production process, as this impacts overall performance and safety.
Quality control ensures that element flatbars perform as expected, which is vital in safety-sensitive applications.
This highlights the necessity of rigorous quality management systems.
Applications of Element Flatbars
Element flatbars play a vital role across various industries due to their diverse applications. They are crucial components in several structures, making it essential to understand their benefits and specific uses. With their versatility, element flatbars adapt to different requirements, providing strength and reliability in various contexts. This section outlines how these flatbars support construction, manufacturing, and structural applications.
Construction Industry Applications
In the construction industry, element flatbars are extensively used for various purposes. They provide essential support in frameworks, beams, and trusses. Their strength-to-weight ratio makes them ideal for use in buildings, bridges, and other structures. Importantly, flatbars can be easily welded or bolted, facilitating the assembly of complex structures.
Key Uses:
- Reinforcement: Element flatbars offer additional stability to concrete structures.
- Support and Framework: They form the basis for frames that hold up walls and roofs.
- Bracing: Flatbars help prevent structural swaying and support wind loads.
Overall, the use of element flatbars is integral to creating safe and durable construction projects.
Manufacturing Sector Uses
In the manufacturing sector, element flatbars find myriad applications. This can be seen in equipment, machinery, and tools where strength and functionality are prime requirements. Their versatility also allows custom shapes, making them valuable in creating specialized parts.
Common Applications:
- Machine Components: Used as bases or supports in milling and cutting machines.
- Fixtures and Jigs: Serve as laid-out support for complex manufacturing processes.
- Conveyors: Adapted as parts that allow for material movement across factory floors.
Element flatbars are significant in streamlining production processes and enhancing efficiency in manufacturing.
Fashioning Structural Components
Element flatbars are also crucial in the fashioning of structural components. They can be cut, bent, or fabricated into necessary shapes for various applications. Industries rely on the adaptability of flatbars to create everything from frames to reinforcements.
Applications in Structural Design:
- Custom Design Elements: Used to create unique supports tailored to specific architectural needs.
- Integration in Systems: Often found in bracing and other critical support systems within larger frameworks.
- Combination with Other Materials: Easily combined with steel, aluminum, and other materials for enhanced strength and appearance.
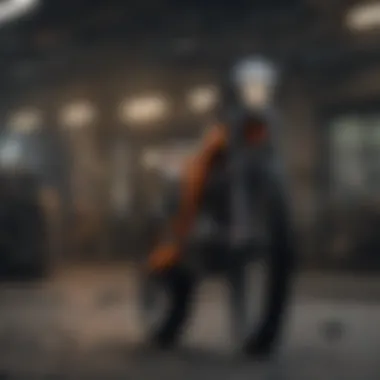
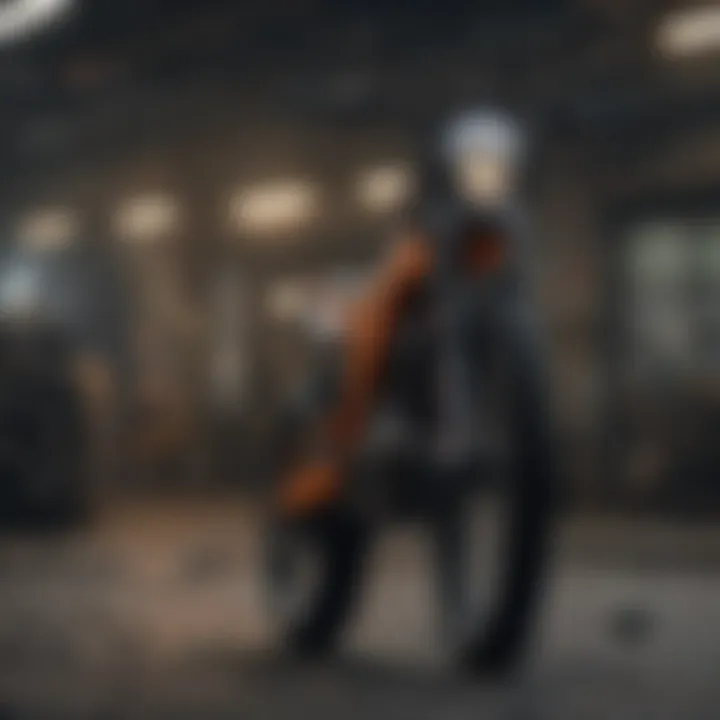
Overall, their ability to be modified allows for innovations in design and functionality, making element flatbars an invaluable resource in shaping structural integrity.
The importance of element flatbars cannot be overstated. Their applications across varied industries illustrate their value as foundational components that enhance both strength and functionality.
Design Considerations
Designing with element flatbars involves several important considerations that ensure functionality, safety, and aesthetic appeal. Each aspect must be carefully evaluated to achieve optimal performance in applications, whether in manufacturing or construction. Understanding these design considerations provides insights into how to utilize element flatbars effectively.
Dimensional Specifications
Dimensional specifications refer to the precise measurements required for element flatbars. These specifications include width, thickness, and length. The importance of adhering to these measures cannot be overstated. Elements that do not meet exact dimensions may lead to structural failure or increased costs in production.
Flatbars can come in various sizes to suit distinct applications. For instance, a six-inch wide flatbar may be suitable for some structural applications, while a two-inch width might be adequate for ornamental work. The choice of dimensions should also consider industry standards, which can guide architects and engineers in their designs.
Moreover, tolerances in dimensions play a critical role in design. A small variation in thickness or width can affect how loads are distributed across the flatbar. Appropriate practices help ensure that the materials selected will meet the projectβs requirements without compromising integrity.
Load-Bearing Capabilities
Load-bearing capabilities are essential when selecting element flatbars for structural applications. The ability of a flatbar to support weight is largely determined by its material properties and its dimensional specifications. Common materials, such as steel or aluminum, provide different load-bearing strengths.
A flatbar must be tested under various load conditions to determine its actual performance. Factors including length, cross-sectional area, and the nature of the loads, whether static or dynamic, affect overall capacity. In many engineering applications, understanding the yield strength and tensile strength of the material will help predict performance behavior.
In practice, engineers often calculate load requirements before installation to ensure safety and stability. Any miscalculation can lead to severe consequences. Therefore, detailed assessment of the flatbarsβ load-bearing capabilities is not just vital; it is a safeguard against potential failures.
Aesthetic and Functional Design
While functionality stands at the forefront of using element flatbars, their aesthetic appeal should not be neglected. The design can influence the overall appearance of a structure while remaining functional. For example, a flatbar that serves as a railing or decorative trim can enhance a space's appearance without sacrificing strength.
Designing with aesthetics in mind means considering finishes and coatings. Many flatbars undergo treatments for corrosion resistance and visual appeal. Finishes can range from simple mill scale to more complex painted surfaces.
Balancing form and function requires careful planning. Designers should collaborate closely with engineers to ensure that the aesthetic choices do not compromise functionality. Thus, this aspect of design contributes not only to visual taste but also to the flatbarβs practical use in its environment.
Advantages of Using Element Flatbars
Element flatbars provide numerous benefits across various industries, establishing them as a substantial choice for many applications. Understanding these advantages is crucial for stakeholders involved in construction, manufacturing, and design. The key advantages include their versatility in use, cost-effectiveness, and ease of installation. Each of these factors contributes significantly to the increasing preference for element flatbars in modern applications.
Versatility in Use
Element flatbars can be utilized across numerous domains due to their adaptable nature. They can be shaped into various profiles, which allows them to function in different contexts.
- Construction: In the construction sector, they are used in framing, support systems, and even decorative elements.
- Manufacturing: In manufacturing, flatbars serve as precursors for complex assemblies, creating frameworks for machines or other equipment.
- Artistic Projects: Artists and designers exploit the aesthetic properties of flatbars to create visually appealing installations and functional art.
Their ability to be customized in size and shape further enhances their versatility. This adaptability makes them suitable for both minor and large-scale projects, offering tailored solutions that meet specific project requirements.
Cost-Effectiveness
Cost considerations are critical in decision-making processes, and element flatbars often present a favorable economic profile. The cost-effectiveness of flatbars can be attributed to several factors:
- Material Distribution: Efficient use of materials minimizes waste, thereby reducing overall costs.
- Long-Lasting: Durable characteristics decrease maintenance needs, which leads to savings over time.
- Bulk Purchasing Options: Many suppliers offer competitive prices for bulk orders, making it feasible to undertake larger projects without overspending.
By reducing expenses without compromising quality, element flatbars provide a viable solution for businesses that aim to stay within budget while delivering high-quality products.
Ease of Installation
The simplicity associated with the installation of element flatbars cannot be understated. This ease influences project timelines and labor costs.
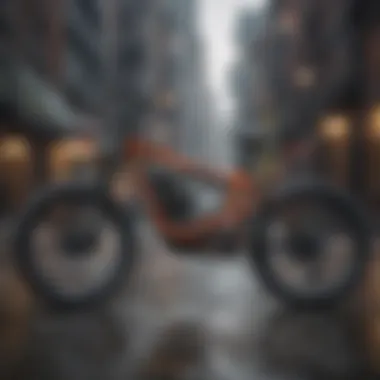
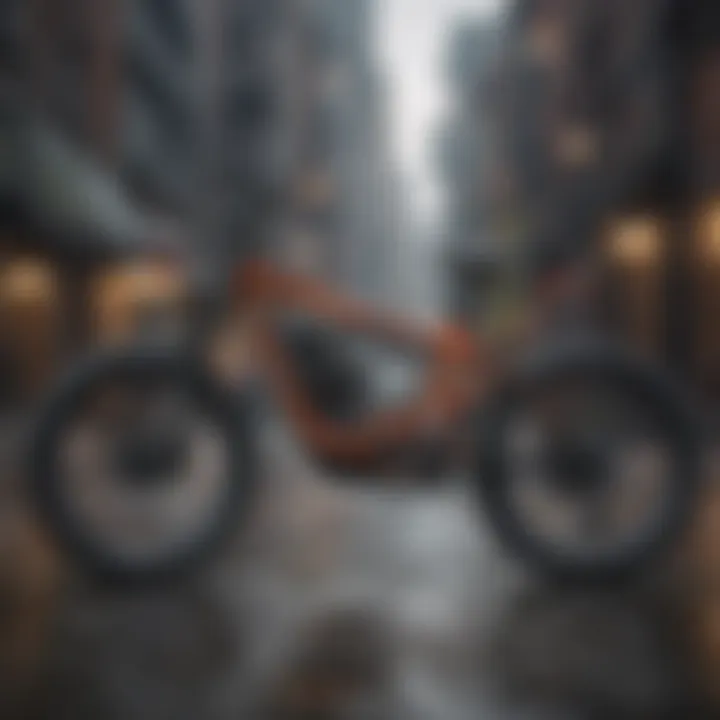
- Lightweight Design: Their lightweight nature facilitates handling and movement, allowing for quick setup.
- Pre-fabrication Opportunities: Many flatbars can be pre-fabricated, which results in even less time spent on-site during installation.
- Compatibility: Their compatibility with various fasteners and hardware makes it easier for workers to implement them into existing structures or assemblies.
Overall, shorter installation times translate to lower labor costs and minimized project delays. This efficacy is particularly advantageous in industries where time is money.
Challenges and Limitations
Issues with Durability
Durability is one of the foremost concerns when employing element flatbars across various industries. The selected materials can dictate performance over time. While many flatbars are manufactured from steel or aluminum, environmental factors significantly influence their longevity. Repeated exposure to moisture, UV rays, and corrosive elements can lead to degradation. Corrosion resistance is crucial in environments where flatbars are subject to harsh conditions. There exist protective coatings that can enhance durability. However, these coatings may themselves wear away over time or require periodic maintenance. Thus, establishing the balance between material selection and environmental resilience is essential for maximizing the lifespan of element flatbars.
Environmental Considerations
The environmental impact of manufacturing and using element flatbars cannot be overlooked. As industries increasingly prioritize sustainability, the choice of materials and processes becomes critical. The production of metal flatbars is energy-intensive and often results in substantial carbon emissions. Material recycling has gained traction, allowing flatbars to be repurposed rather than discarded. This tactic addresses waste management concerns while conserving raw materials. Furthermore, considerations like energy consumption during manufacturing are important to evaluate. Hence, recognizing the implications of these elements is vital for responsible industry practices.
Regulatory Compliance
Navigating regulatory compliance presents another layer of complexity in the use of element flatbars. Different regions have established codes and standards to ensure safety and durability in construction and manufacturing. Regulations often dictate material specifications, performance testing, and safety protocols. Non-compliance can lead to serious repercussions, including potential project delays or increased liability. It becomes imperative for industry professionals to stay informed about the latest legal frameworks. This ensures that flatbars are correctly utilized and that end-users are safeguarded from structural failures. Awareness of these requirements must be ingrained within project planning and execution, emphasizing the importance of adherence to regulatory obligations.
Future Trends in Element Flatbars
The future of element flatbars is pivotal for industries reliant on structural components. Understanding upcoming trends enhances strategic planning and innovation adoption. As markets evolve, so do the materials and technologies driving these fundamental elements. Each progress contributes to enhancing performance and sustainability.
Innovations in Materials
Material development plays a crucial role in the future of element flatbars. New alloys and composites are gaining attention for their strength and durability. For instance, advancements in high-strength low-alloy steels improve load-bearing capabilities while reducing weight. These innovations allow for lightweight construction, enhancing efficiency without compromising safety.
Another key area is sustainability. Many manufacturers are focusing on recycled materials. This aligns with global efforts to reduce waste. By using recycled metals, companies can lower their carbon footprint and advance eco-friendly initiatives.
Technological Advancements
Technological advancements shape the production and application of element flatbars. Automation in manufacturing processes is leading to increased precision and consistency. Techniques like laser cutting and CNC machining provide exceptional accuracy, which is vital in structural applications.
Moreover, the role of digital design software cannot be overstated. Programs that simulate real-world loading and stress conditions help engineers create better designs from the start. This reduces material waste and enhances the product's overall performance.
Key Benefits:
- Enhanced precision in cut and design.
- Expanded capabilities for complex shapes and uses.
- Reduction in production time and costs.
Market Trends and Projections
Understanding market trends helps stakeholders anticipate changes in demand and adapt strategies accordingly. The construction sector is showing increasing interest in integrated designs combining element flatbars with other materials. This trend points to a shift toward hybrid solutions that enhance structural integrity and aesthetic appeal.
Forecasts indicate a steady growth in the demand for element flatbars over the next decade. As urbanization continues, the pressure for efficient construction materials will rise.
- Market Drivers:
- Urbanization and infrastructure development.
- Increasing focus on sustainable building practices.
- Demand for advanced structural components in manufacturing.
Overall, staying informed in these areas ensures that industries utilizing element flatbars can adapt swiftly to changes and capitalize on new opportunities.
The End
The conclusion of this article underscores the significance of understanding element flatbars in various sectors. Recognizing their construction, applications, and benefits is essential for professionals and enthusiasts alike. Element flatbars have become integral components, extending far beyond simple metal rods. Their versatility allows them to adapt seamlessly to a variety of roles, making them indispensable in modern constructions, manufacturing processes, and design.
Summary of Key Points
- Definition and Characteristics: Element flatbars are defined by their solid, elongated shape, typically available in various widths, lengths, and thicknesses. They offer strength and rigidity which make them suited to numerous applications.
- Materials and Production: Different materials such as steel or aluminum are used to manufacture flatbars, often chosen based on the specific application and required properties. Production techniques ensure that quality standards are met.
- Application Areas: The construction and manufacturing industries utilize element flatbars for structural integrity, machinery foundations, and support frameworks.
- Design Considerations: Dimensions must be precise, accommodating load-bearing capabilities while also considering aesthetic elements when applicable.
- Advantages: In addition to versatility and cost-effectiveness, ease of installation adds to their attractiveness as a building material.
- Challenges: Issues surrounding durability and environmental factors can affect the selection and use of flatbars. Compliance with regulatory standards is particularly crucial in construction projects.
- Future Trends: Innovations in materials and technological advancements promise to further enhance the functionalities and applications of element flatbars.
Call to Continued Exploration
Engaging with the topic of element flatbars invites ongoing inquiry into their multifaceted applications and emerging trends. The industries they support are constantly evolving, and staying informed about innovations is vital for anyone involved in construction and manufacturing. Examining the interplay between new technologies and traditional materials can lead to discoveries that enhance efficiency and reduce environmental impact. Readers are encouraged to delve deeper into industry publications and join discussions on platforms such as reddit.com or facebook.com to exchange insights and experiences.
The understanding of element flatbars is not merely an academic exercise; it reflects the core of modern engineering practices. Their relevance in various applications ensures they will remain a focal point of exploration and innovation in the years to come.